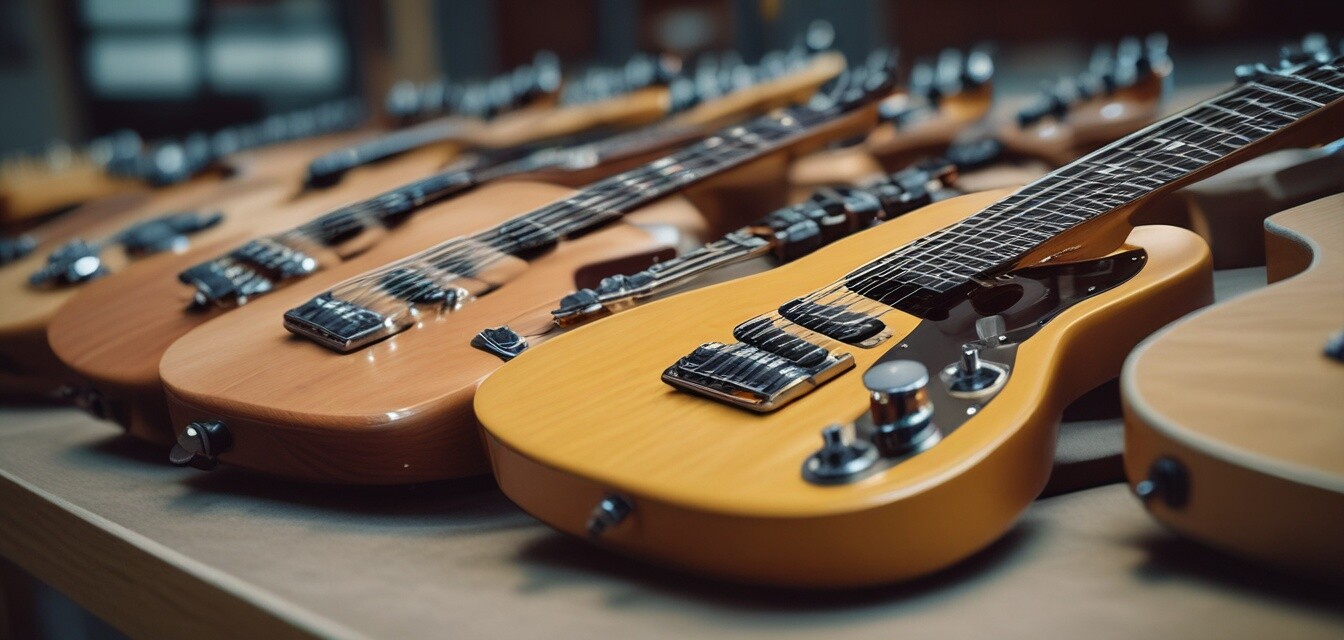
Behind the Scenes: Fender Guitar Manufacturing Process
Key Takeaways
- Fender guitars are crafted using precision engineering and quality materials.
- The manufacturing process includes multiple stages: selection, machining, and final assembly.
- Technological advancements have enhanced production efficiency while maintaining traditional craftsmanship.
- Each Fender guitar is unique, showcasing the brand's commitment to quality.
- Understanding the manufacturing process can enhance your appreciation of Fender guitars.
Fender guitars have long been celebrated for their exceptional quality and sound. Behind every iconic guitar lies a meticulous manufacturing process that blends traditional craftsmanship with modern technology. This article will delve into the intricate steps involved in producing Fender guitars, highlighting the skills and materials essential to their creation.
The Anatomy of a Fender Guitar
Before we explore the manufacturing process, it is crucial to understand the components that make up a Fender guitar. Here’s a brief overview:
Component | Description |
---|---|
Body | The main structure that resonates the sound. |
Neck | Holds the frets and strings and is crucial for playability. |
Headstock | Holds the tuning pegs and gives the guitar its balance. |
Pickups | Convert string vibrations into electrical signals. |
Bridge | A component that anchors the strings and influences tone. |
The Manufacturing Process
The journey of crafting a Fender guitar encompasses several stages, each vital to achieving the signature tone and aesthetic that Fender is known for.
1. Selection of Materials
Quality starts with the materials. Fender is known for using high-grade wood types which contribute significantly to the sound and durability of the instrument. Here are some common materials used:
- **Alder**: Often used for the body, it provides a balanced tone.
- **Mahogany**: Known for its warm sound, commonly used in necks.
- **Maple**: Offers a bright tone and is often used for necks and tops.
2. Machining
Once the wood is selected, it goes through precision machining. This involves:
- Cutting the body and neck to shape.
- Routing cavities for pickups, electronics, and other components.
- Shaping the neck for comfortable playability.
3. Joining the Body and Neck
After individual parts are shaped and routed, they are joined together. The neck is meticulously attached to ensure perfect alignment and sustain.
4. Assembly
The next phase involves installing hardware and electronics:
- **Pickups**: Installed in the routed cavities.
- **Bridge and Tuning Machines**: Essential for string tension and tuning stability.
- **Electronics**: Volumes and tone controls are wired for optimal performance.
5. Finishing Touches
Each guitar is then sanded, stained, and finished. This not only enhances the beauty but also protects the wood. The finishing process can include:
Finish Type | Description |
---|---|
Lacquer | Provides a thin, glossy finish that enhances the wood’s natural feel. |
Polyurethane | A more durable finish that is resistant to wear and tear. |
Oil | Allows the wood to "breathe" and feel more natural in the player's hands. |
6. Quality Control
Every guitar undergoes rigorous testing and quality control to ensure it meets Fender's high standards. This includes playability tests, sound checks, and visual inspections.
Tips for Guitar Enthusiasts
- Try different models to understand how materials affect sound.
- Explore the differences between finishes and how they impact playability.
- Stay updated with the latest Fender news and releases at our News and Trends section.
Conclusion
Understanding the comprehensive manufacturing process of Fender guitars not only deepens your appreciation for these instruments but also helps you make informed choices when selecting your next guitar. With a dedication to quality craftsmanship and innovation, Fender continues to lead the way in the guitar world.
Pros
- Exceptional craftsmanship ensures high-quality instruments.
- Diverse range of materials offers unique sound characteristics.
- Innovative technology enhances the overall guitar performance.
Cons
- Higher price point compared to some other brands.
- Some models may require a break-in period for optimal sound.